The Global Chip Shortage: How to Get Through 2022
For months, the news has been full of stories around component supply shortages and their wider impact. Analysts at Goldman Sachs found that over 160 different industries were affected by the crisis¹. Tech giants issued warnings about disruption to production. Though some are reported to be defying the component crunch, such as Tesla², others are still facing issues – for instance automotive industry brands such as Toyota³ and Ford4.
ByteSnap Director Dunstan Power assesses the global chip shortage situation and shares some practical steps to keep product design moving this year.
Chip shortage situation backdrop
Coronavirus hit the electronics industry, with shut downs in 2020. This was made worse by a huge increase in consumer demand, partly due to people spending money on personal electronic goods to relieve boredom when in lockdown at home.
In addition, the surge in electric vehicle adoption is adding to a perfect storm, with the automotive industry now accounting for approximately 10% of chip demand.
On top of that, natural disasters further exacerbated the situation; for example, water shortages in Taiwan caused by drought5. As the country makes a high proportion of the world’s most sophisticated chips, this disruption simply compounded Taiwan’s chip production and ability to supply.
Also, fires at facilities have been a problem; most recently a blaze6 at a plant in Germany which makes essential equipment used in chip production raised fears of added strain to the components supply chain.
Ripple effect of the electronics component shortage
It’s not just silicon chips that are being hit by supply chain disruption.
Raw materials, metals and plastics are difficult to source from a supplier able to guarantee lead times. Thus, the impact of the chip shortage continues to reverberate across the entire electronics and product manufacturing industries globally.
Inevitably, prices will rise – via three different of price increase scenarios:
- Straight-forward capitalism – with chip manufacturers deciding to “make hay while the sun shines” in the face of what many consider to be unprecedented demand and simply charge more for parts
- Disincentives to prevent hoarding – chip vendors applying temporary price increases to discourage hoarding.
- Outright profiteering – where intermediaries are exploiting the crisis by buying components at reasonably low prices and the selling excess stock at extortionate rates – as high as a hundred times regular market prices.
Of course, the hope is that, in time, the profiteering element will reduce. However, it seems likely that higher chip prices will be with us for the foreseeable future, certainly for a large part of 2022 – at least until there is some real long-term competition to drive prices down again.
This begs the question – how can product managers and engineering teams overcome the challenges of the chip shortage and continue accelerating design projects?
Let’s go through some practical steps that should help keep your product development process moving this year and beat the worst of the electronics components crunch.
7 Steps to Designing Around the Global Chip Shortage for 2022
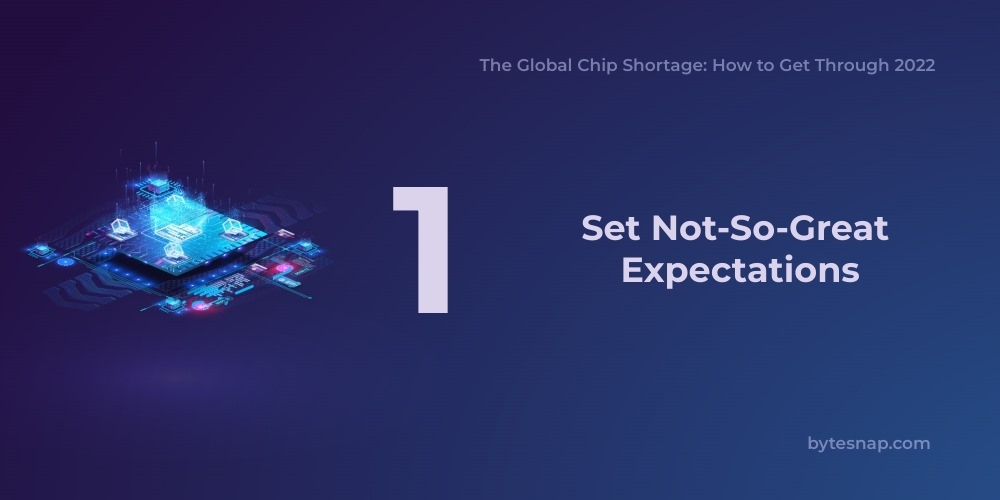
1. Adjust Your Expectations
Firstly, there’s a very necessary expectation adjustment; a paradigm shift where the market has to adapt to price increases – and, unfortunately, adjust to paying more for components.
There will inevitably trickle down to the consumer with price increases, because there’s a limit to how far one’s margins can get squeezed before business becomes unviable.
From an electronics design point of view, it’s all about designing to be as flexible as possible.
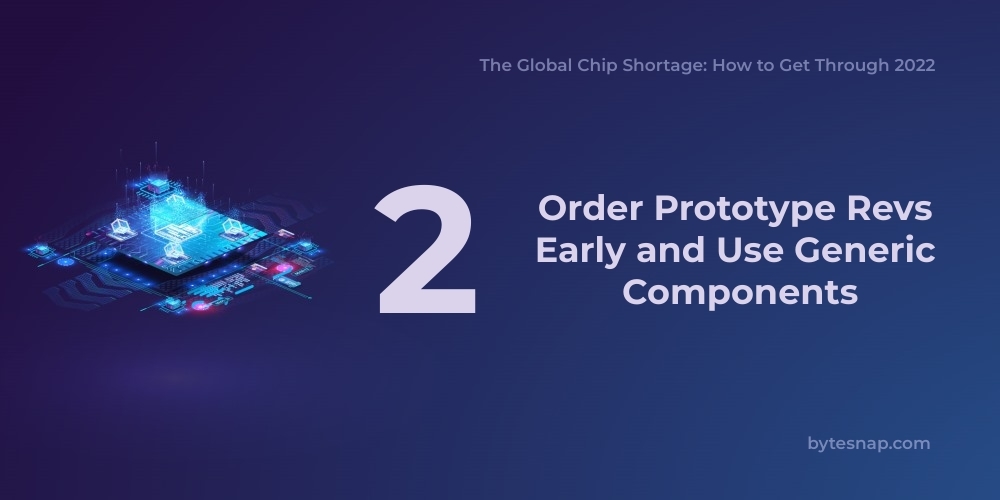
2. Order prototype revs early and use generic components
We recommend designing in components that are as generic as possible, so that they can be substituted.
In terms of prototypes, order all revisions in the early stages of the design process – as early as possible – rather than waiting until manufacturing time, because even getting small quantities can be tricky.
For example, for five revision As, five revision Bs and five revision Cs, 15 off of stock should be ordered at the start of the project on the assumption that the stock may be lost to others or not all needed. This approach has certainly paid off for us.
Obviously, generic parts cannot always be used; there are many components that deliver specific functionality. In that case, some chip manufacturers have been hit harder than others.
Identifying companies with a good record in supplying and not obsoleting components is a must (more on this later). They may list shortage manufacturing lead times on their websites. Armed with this information, design teams may need to use more expensive components.
Checking availability at this point of design is critical, rather than designing a chip in early without confirming lead times.
In the past, obsolescence checks would have been sufficient to ensure parts were active. Now, however, more detailed market research – e.g., looking at manufacturing lead times at the point of design – is vital.
Example
Here’s a real-world example:
- An engineer is designing one type of microcontroller, which is cheap and costs £1.50, while another vendor has a similar performing product for £2.50.
- On reaching production, the £1.50 part is unavailable. The engineer may head to the grey market, or to those specialising in hard-to-find components. Here the seller will offer a price of £8.00.
- The engineer is then paying £8.00 for £1.50 component – whereas, if the £2.50 component had been designed in at the start, the price would have been set there and then.
- The result: a final product where the price is more predictable, and that is possible to manufacture – rather than something which may be cheaper to put together but will be troublesome in production due to the uncertainty of supply in a wildly fluctuating components market.
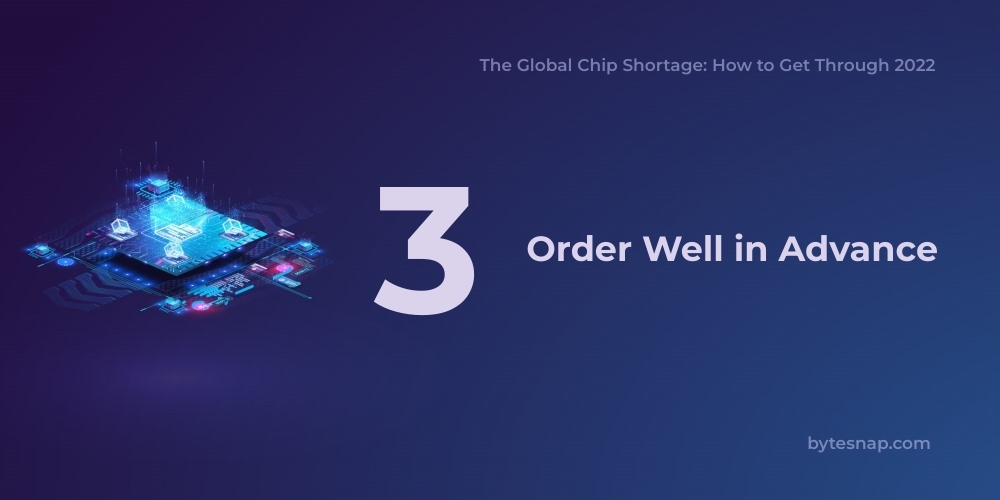
3. Order well in advance
Semiconductor suppliers are typically giving 90-day cancellation terms at the moment. This will vary from vendor to vendor, and the aim here is to discourage overordering and submitting the same order with multiple suppliers.
With components on allocation, businesses are only receiving approximately 20-40% of their original order. For instance – a distributor that orders 100,000 chips and may end up with 30,000 which it will split amongst its customers.
Suppliers are also insisting on payment terms encouraging advance orders to help with manufacturing volumes. In the past, there may have been harder cancellation terms, therefore buyers were discouraged from putting in long term orders, which consequently meant that vendors had less visibility of customers’ needs.
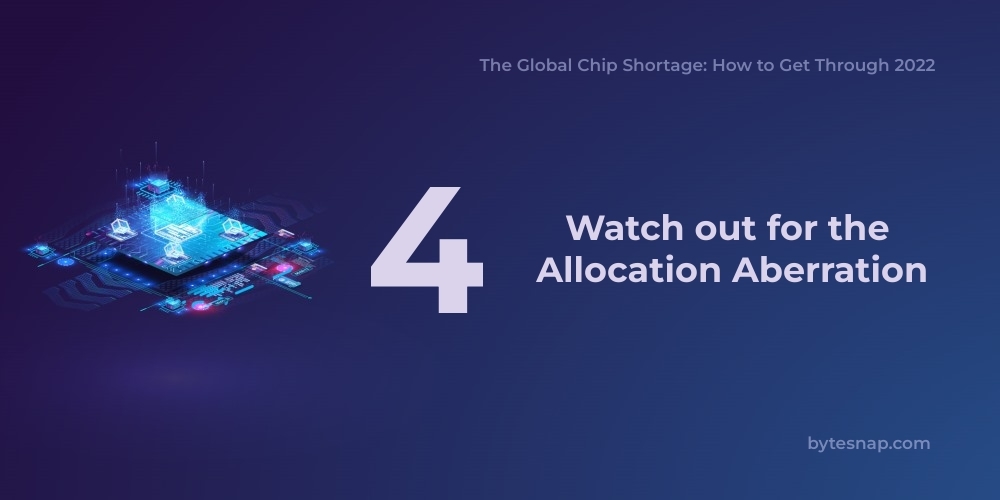
4. Watch out for the Allocation Aberration
Of course, there are always attempts to cheat the system.
Some buyers, knowing that they will only get 20% allocation, are approaching five different distributors and asking for the same thing, on the basis that they only think that they’ll get a fifth from each distributor.
However, those buyers could end up with the original full allocation five times over.
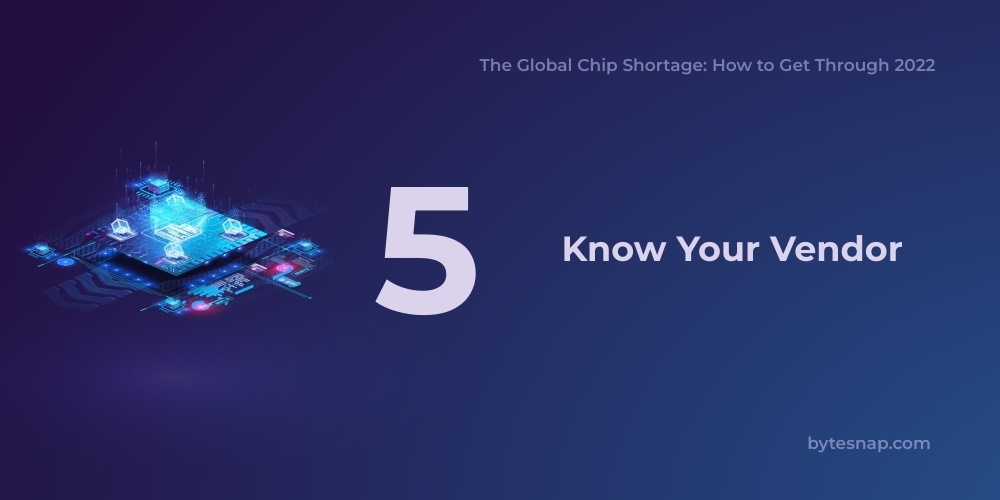
5. Know your vendor, remember your longevity due diligence
Checking out a vendor’s supply record is a crucial step when planning your electronic designs around the chip shortage.
At ByteSnap, we’ve come across some semiconductor vendors who have not and do not plan to supply obsoleting parts. Recognizing the different vendors for their stance on obsolescence is the mark of a good electronics team or consultancy. Our clients pay us for that industry knowledge to further safeguard product development.
Engineers face running into problems when lines are switched over. These manufacturers only have a limited amount of silicon to work with and must allocate that silicon to their various chips. For instance, if there is high demand on one chip, a lot of wafers will be allocated to it, while one with lower demand will be assigned fewer wafers.
Consequently, if the chip maker has made concrete longevity plans on a part, at least stock will be allocated – albeit, on a long lead time.
Whereas, if a vendor has no longevity plan, they might just say, “I’m just going to obsolete this part because it’s not in demand and everyone’s buying this other part, so let’s focus on something else instead. I’ll just obsolete this with a short notice…” This has happened in our experience where devices were just obsoleted at very short notice.
Be sure to identify companies with good longevity plans – where, for example, they confirm that the part will be available for a set amount of time.
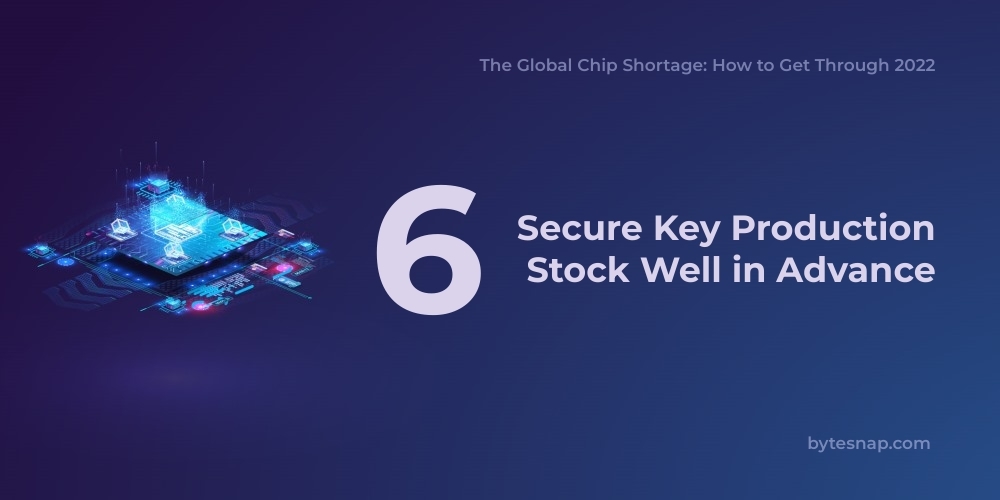
6. Secure key production stock ahead of project start
To overcome the chip shortage, some of our customers are securing key stock, such as microcontrollers, before starting the design of production. To clarify, this may not be the best course of action for start-ups, as new businesses tend to have very uncertain sales volumes.
Early securing of stock does makes sense, however, for an established company developing a next generation product with known sales volumes – for example, 100,000 were sold last year, and are predicted to sell 100,000 next year.
Normally, companies would steer away from this approach, because engineers may get part way through development and decide the part isn’t up to scratch, and it’s not doing the job. But, during this current chip shortage, buying in advance pays. This is because a commitment on a key component at the start of a project ensures that you are in good shape at the end; all other parts and materials, can be managed along the process.
Engineers can sleep easy knowing that software development – which is a huge cost in terms of the writing the code, and, in particular, testing – is safe, because the microcontroller supplies are secured. Microcontrollers are a key component to secure as major software effort is necessary for them and to redevelop software can have a huge impact on project timescales and budget.
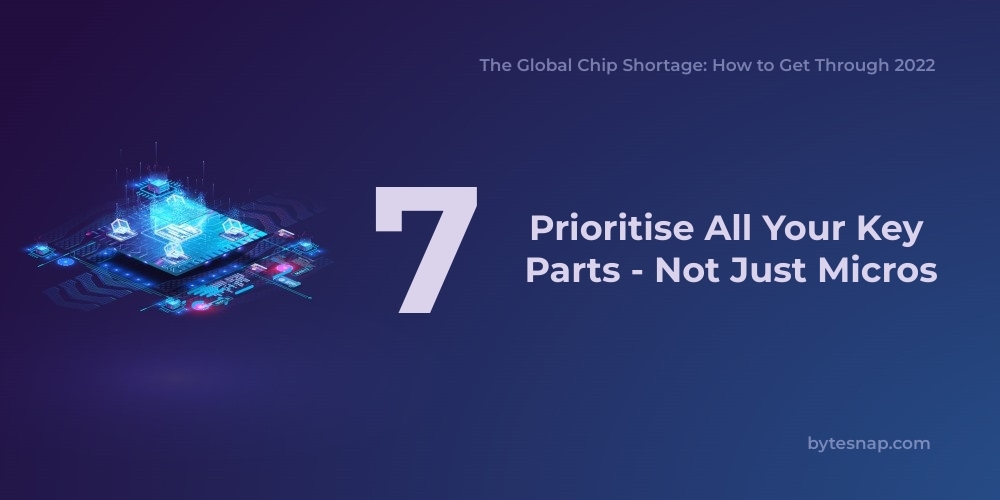
7. Remember the key parts are not just microcontrollers
Also remember to prioritise any power supply chips associated with your chosen microcontroller, because they are subject to very long lead times currently. The PMICs that are used for some of these micros are also very hard to secure.
If you’ve got a particular core part of your design, it might be worth at the outset trying to buy that stock or secure it; not necessarily get it delivered to your door, but to protect that stock allocation at the outset.
That way, all your software development is safe.
Conclusion
In summary, follow these tips to help minimise the effects of the chip shortage on your design projects:
- Adapt your expectations to the current market conditions
- For prototypes, order revisions as early as possible
- Consider generic parts for your existing product/product upgrades
- Check the lead times at the point of design
- Analyse vendors’ stance on supply and obsolescence
- Order well in advance: secure key production stock ahead of project start
- Safeguard software development by securing any power supply chips (PMICs), with your microcontrollers
But it’s not all doom and gloom. Chip vendors are doing very good business at the moment and some of that profit will find its way into new R&D.
Also, there new capacity coming into the market; not all in China either in a very buoyant market, with demand outstripping supply.
The electronics industry just needs to weather this chip shortage storm with the same resilience shown during lockdown to ensure that we continue to innovate and deliver products to market.
Further Reading
[3] https://japantoday.com/category/business/toyota-yearly-production-target-hit-by-chip-shortage
[4] https://edition.cnn.com/2021/01/11/tech/ford-plant-shutdown-computer-chip-shortage/index.html
[5] https://fortune.com/2021/06/12/chip-shortage-taiwan-drought-tsmc-water-usage/
[6] https://www.reuters.com/technology/asml-reports-fire-its-berlin-factory-2022-01-03/
Need support to get your designs through the components shortage?
We’re helping businesses navigate through parts supply issues to push through and complete product designs during this unprecedented time.
We’re ready to help you too – let’s talk: